Opening the Possible of Aluminum Spreading: A Comprehensive Review
Aluminum casting stands as a foundation in the world of metalworking, providing a plethora of advantages and applications throughout numerous industries. As we browse via the landscape of aluminum casting procedures and delve into the details of quality control steps, a thorough overview of unlocking the real possibility of this metal emerges.
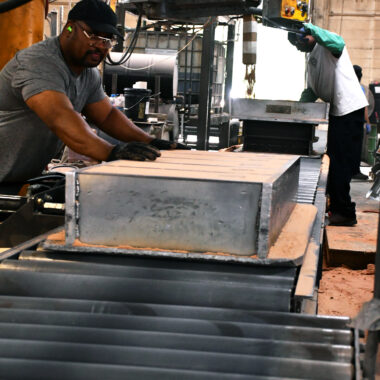
Background of Aluminum Casting
Aluminum spreading has an abundant historical history that goes back to ancient civilizations, showcasing the sustaining significance of this metallurgical process in numerous industries. When ancient civilizations like the Egyptians and the Sumerians made use of simple methods to cast little objects, the origins of aluminum casting can be mapped to about 5,000 B.C.. It was not up until the 19th century that aluminum casting saw substantial improvements with the discovery of the Hall-Héroult process for removing aluminum from its ore, making it more easily accessible for casting purposes.
During the Industrial Change, aluminum casting obtained widespread popularity as a result of the metal's lightweight residential properties and rust resistance. This led to its substantial usage in manufacturing parts for different sectors, including automobile, aerospace, and building. The convenience of light weight aluminum casting enabled for complex layouts and complex shapes to be generated with accuracy, better fueling its adoption throughout different markets. Today, light weight aluminum spreading remains to be a cornerstone in the production of a vast array of products, highlighting its enduring tradition and value in modern-day production procedures.
Benefits and Applications
With its extraordinary strength-to-weight ratio and exceptional thermal conductivity, aluminum spreading uses a myriad of benefits and diverse applications across numerous industries. One of the main benefits of light weight aluminum casting is its light-weight nature, making it an optimal selection for industries where weight reduction is critical, such as automobile and aerospace.
In terms of applications, aluminum casting is extensively made use of in the vehicle market for elements like engine blocks, cylinder heads, and wheels due to its stamina and light-weight buildings. The versatility of light weight aluminum spreading prolongs to consumer electronic devices, where it is made use of in the production of casings and heat sinks.
Kinds Of Light Weight Aluminum Casting Procedures
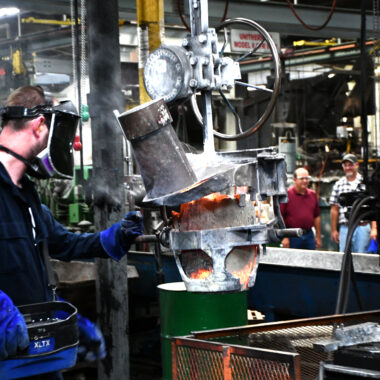
Among the numerous methods used in industrial setups, light weight aluminum casting procedures include an array of methods matched to various applications and needs. Investment spreading, likewise recognized as check it out lost-wax spreading, is favored for its capacity to generate detailed and detailed parts with a smooth surface area finish. Each of these light weight aluminum casting processes uses unique benefits, catering to a wide range of commercial demands.
Developments in Aluminum Casting Techniques
Current innovations in light weight aluminum casting methods have actually changed the production sector, providing enhanced performance and accuracy in the production of complicated components. One significant advancement is the growth of 3D sand printing innovation, which enables the creation of intricate sand molds with very little manual work. This strategy permits higher layout adaptability and faster production cycles, making it excellent for prototyping and tiny set production.
In addition, making use of innovative simulation software application has significantly enhanced the casting process by allowing designers to optimize mold designs and predict potential problems prior to manufacturing begins (casting aluminum). This leads to improved item quality and minimized product waste
Furthermore, the adoption of vacuum-assisted aluminum my blog casting has actually improved the overall high quality of spreadings by decreasing porosity and making certain an extra uniform distribution of liquified metal. This strategy is specifically valuable for components that need high structural stability and premium surface coating.
Quality Assurance in Light Weight Aluminum Spreading
The improvements in light weight aluminum casting strategies have not just boosted efficiency and accuracy however have likewise emphasized the essential value of quality assurance in ensuring the integrity and performance of actors components. Quality assurance in aluminum spreading involves an organized approach to examine the manufacturing and keep track of process, identifying any discrepancies from established requirements that could affect the end product.
One vital element of quality assurance is making use of advanced modern technologies such as non-destructive testing methods like X-ray and ultrasound why not check here to spot interior flaws without endangering the stability of the actors components. In addition, applying strenuous inspection protocols at numerous stages of production assists in recognizing and remedying problems promptly, making certain that only elements meeting the specified standards are released for use.
Additionally, quality assurance extends past the production procedure to include post-casting treatments like warm treatment and surface ending up, ensuring that the end products fulfill the preferred requirements. By prioritizing quality assurance measures, manufacturers can boost item consistency, resilience, and overall customer satisfaction in the realm of aluminum casting.
Final Thought
Various kinds of casting processes and cutting-edge strategies have been developed to enhance the performance and quality of aluminum spreading. In general, light weight aluminum spreading continues to be a useful production procedure with excellent possible for additional innovations in the future.
As we navigate with the landscape of light weight aluminum casting procedures and delve into the complexities of high quality control actions, a detailed overview of opening the real possibility of this metal emerges. It was not up until the 19th century that aluminum spreading saw significant advancements with the discovery of the Hall-Héroult process for extracting light weight aluminum from its ore, making it much more available for casting objectives.
Amongst the different approaches utilized in commercial settings, light weight aluminum casting processes incorporate a variety of techniques matched to various applications and requirements. Financial investment casting, additionally recognized as lost-wax casting, is favored for its capability to create detailed and thorough components with a smooth surface area coating. Different types of casting procedures and ingenious strategies have been established to boost the efficiency and high quality of light weight aluminum spreading.